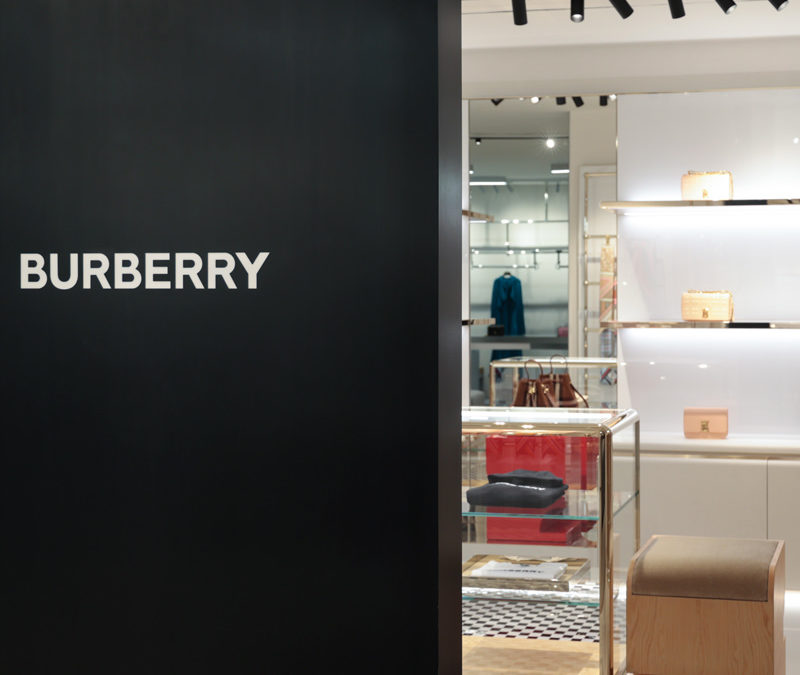
A NEW CORNER FOR BURBERRY
Quickly and with a structured time schedule, a Corner of the Tiziana Fausti store in Bergamo was replaced by a new brand.
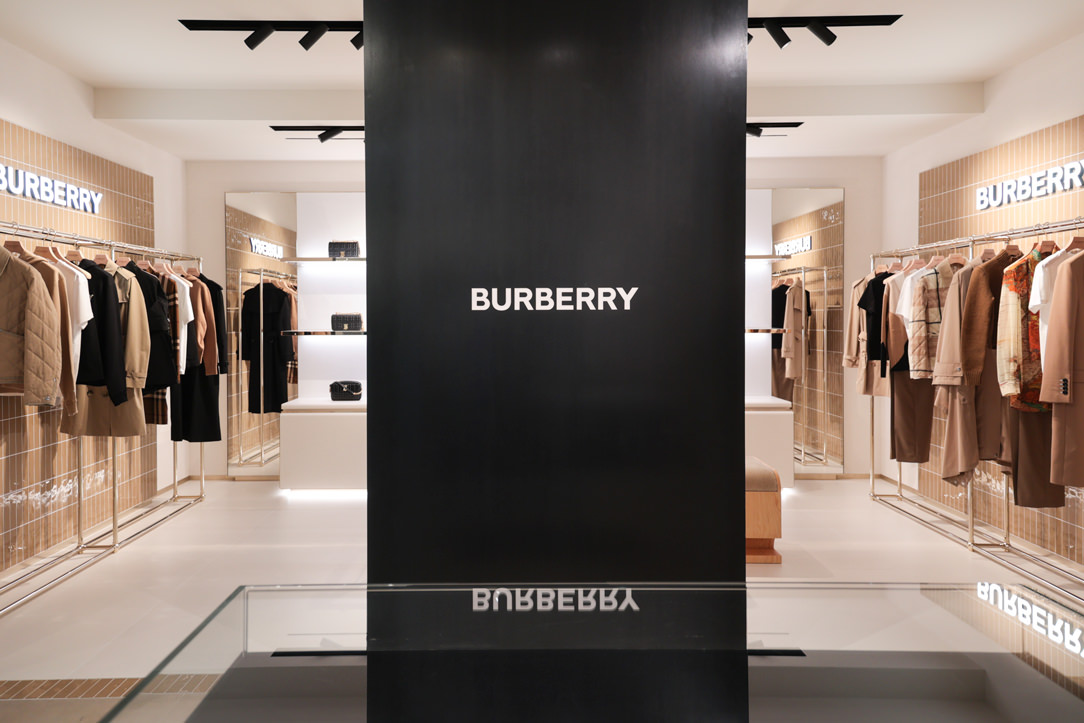
CORNERS AND FASHION
introducing the concept of Corners we can say that they are single-brand exhibition spaces and are a mirror of the products displayed inside them.
In fact, Designers and Architects linked to the Fashion Atelier are working hardly to express the identity and image of the Brand.
The corners are used by the Brand to facilitate the direct control in terms of assortment, sales staff and visual merchandising.
Furthermore, Brand Loyalty improves, and the consumer is able to more clearly distinguish the value of the brand and the product they are going to buy.
However, a Corner has a short duration, of a few years, and is then usually updated or replaced.
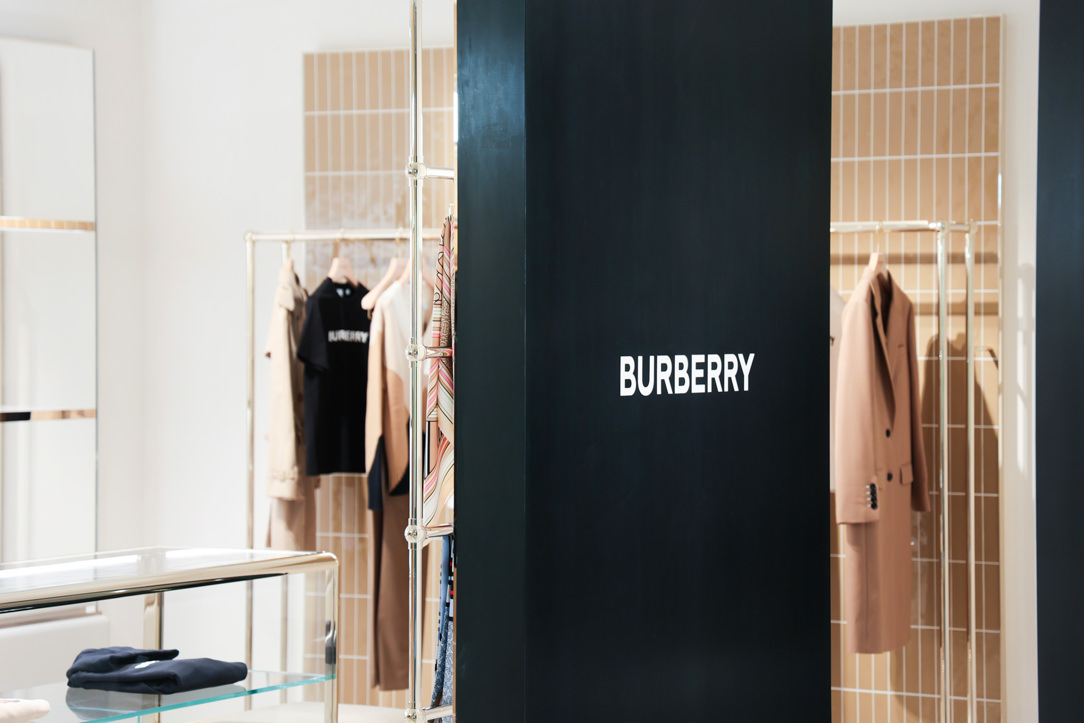
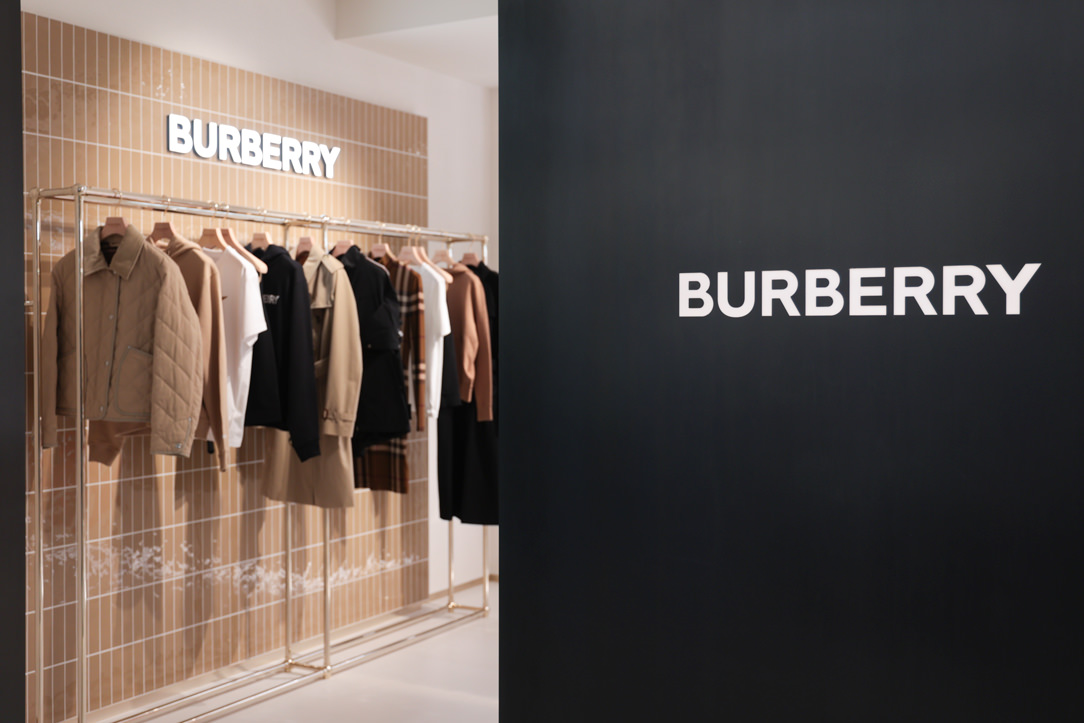
CREATION OF A WHITE BOX FOR BURBERRY
In this case, after a few years, it was decided to replace the Corner of the Brand Stella McCartney in the Tiziana Fausti store with the Burberry one.
Once the change was defined, the Architects of the Maison had presented a design of the space, which was then approved by the property.
Usually, the furnishings of the Brand are supplied by a chosen company that takes care of all the dedicated Retail spaces.
Our task was therefore to create a White Box, which we also talked about in our old article, and to act as General Contractor.
All the useful actors for the replacement of the Corner were then recruited and the process followed step by step.
THE WORK SCHEDULE
Once defined the changes and the new arrangements to be created, the work scheduling as followed.
The replacement of a Corner must be quick so as not to preclude the normal sales trend of the shop.
The agreed program in fact included no more than two weeks of work. When the X date arrived, the Corner was isolated with a varnished wooden closing barrier, to preserve the nearby spaces from dust and allow a normal flow within the interested area.
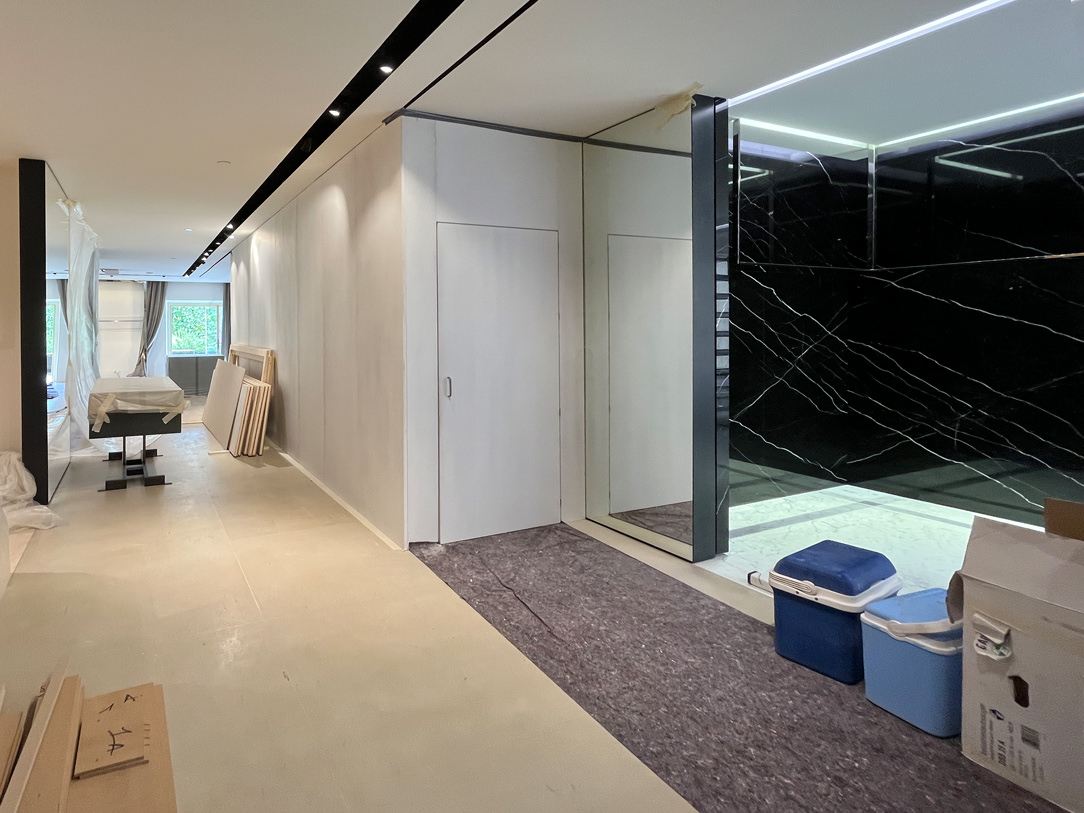
These began with the laying of the floor as a work of art, followed by the grouting, the first coat of primer on the walls and the change of the light tracks on the ceiling.
On the outside, the full-height black panel of the old Brand has been replaced with that one of Burberry, its logo laser cut and backlit by an opal plexiglass.
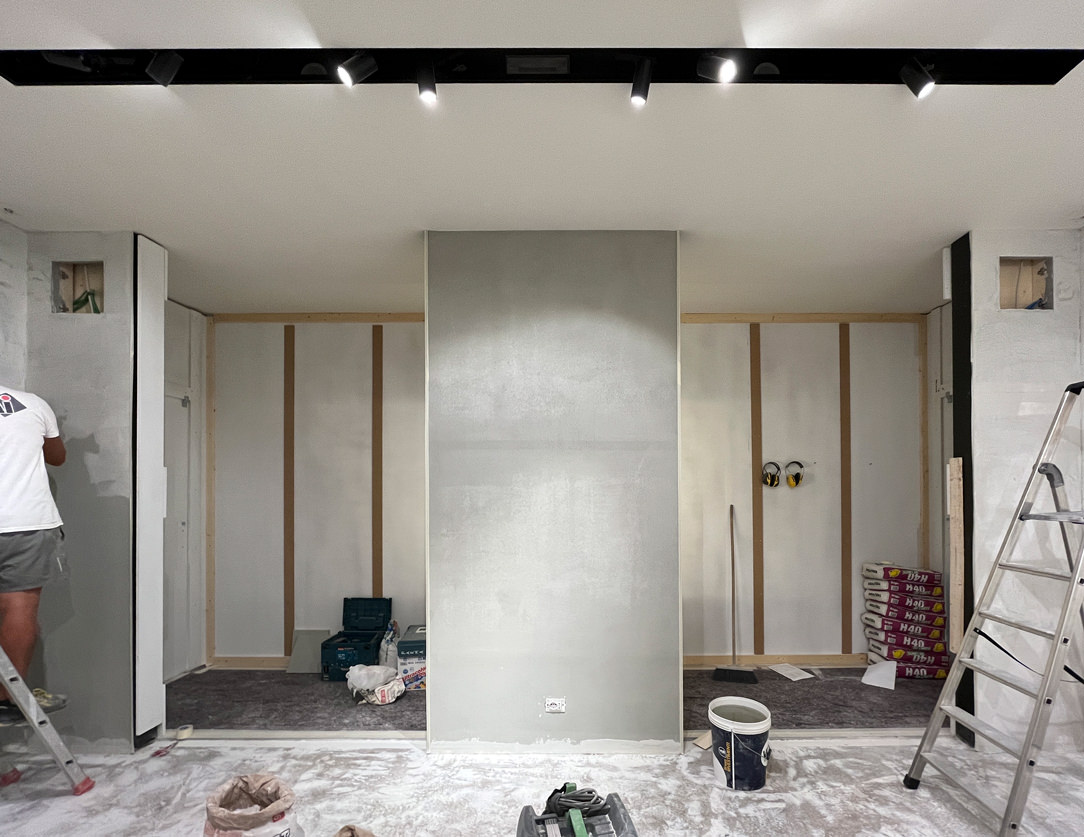
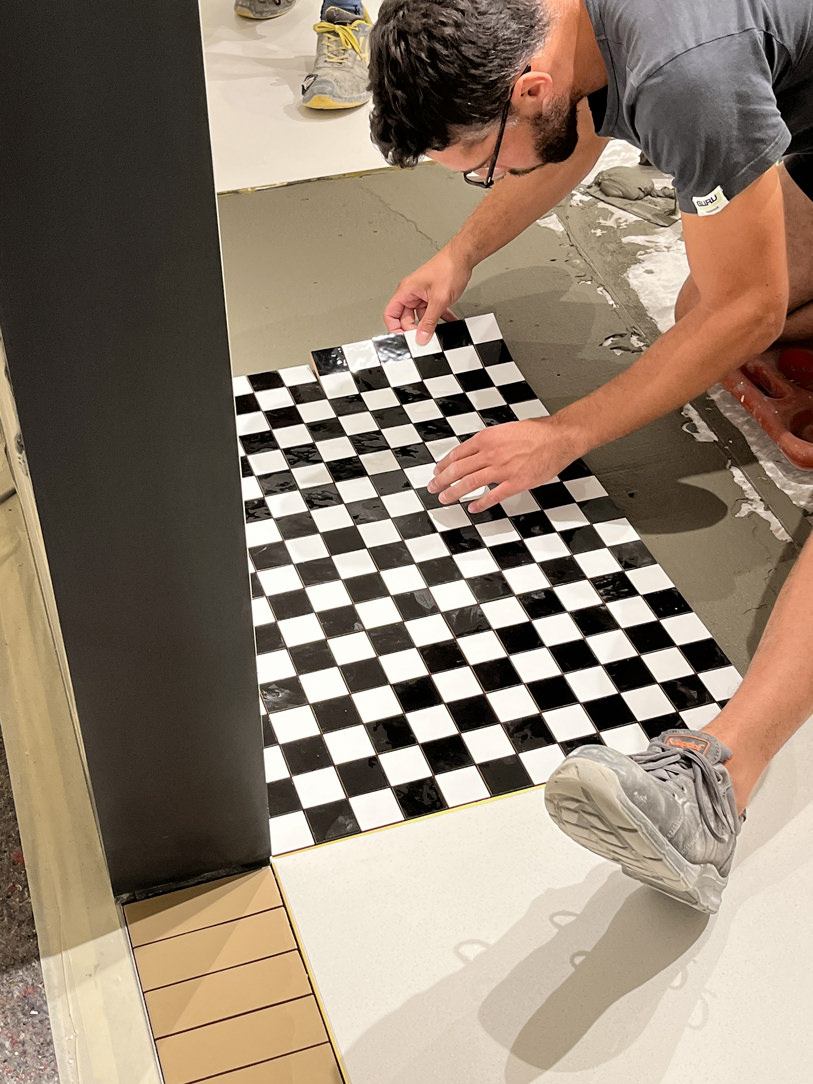
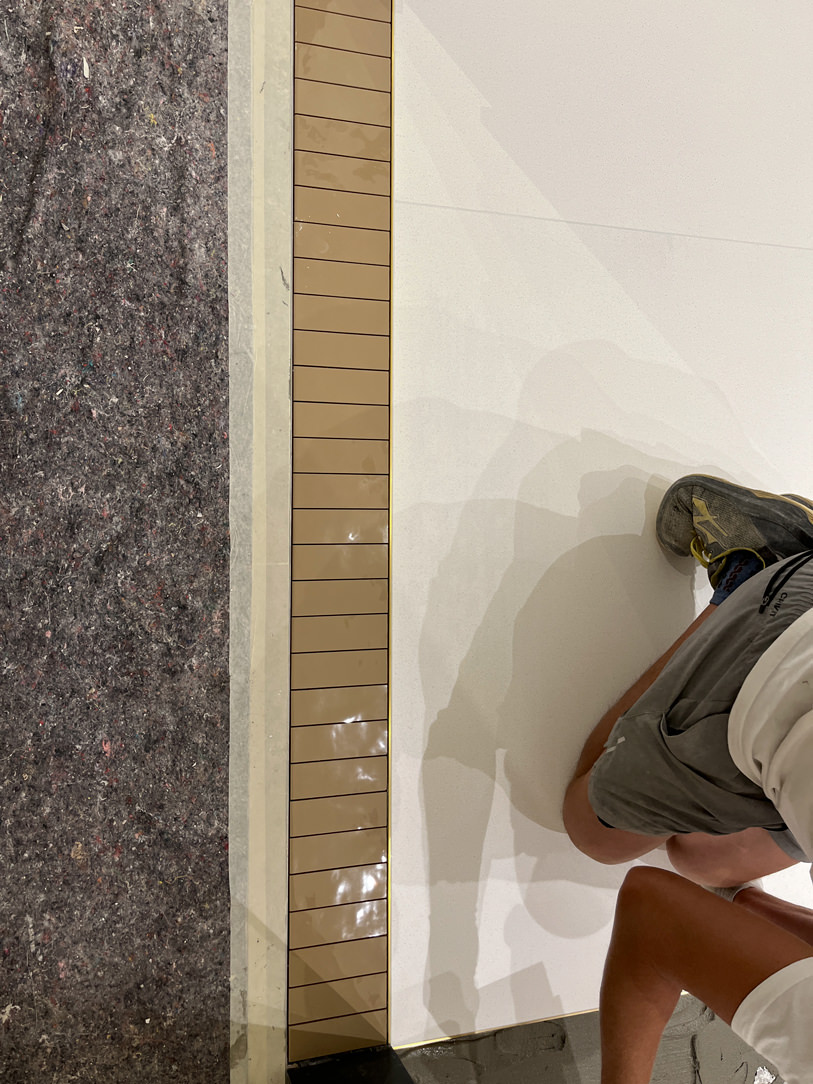
At the end of the first week, the White Box was completed and all the electrical arrangements, including those for the illuminated sign on the wall, ready for the next actors.
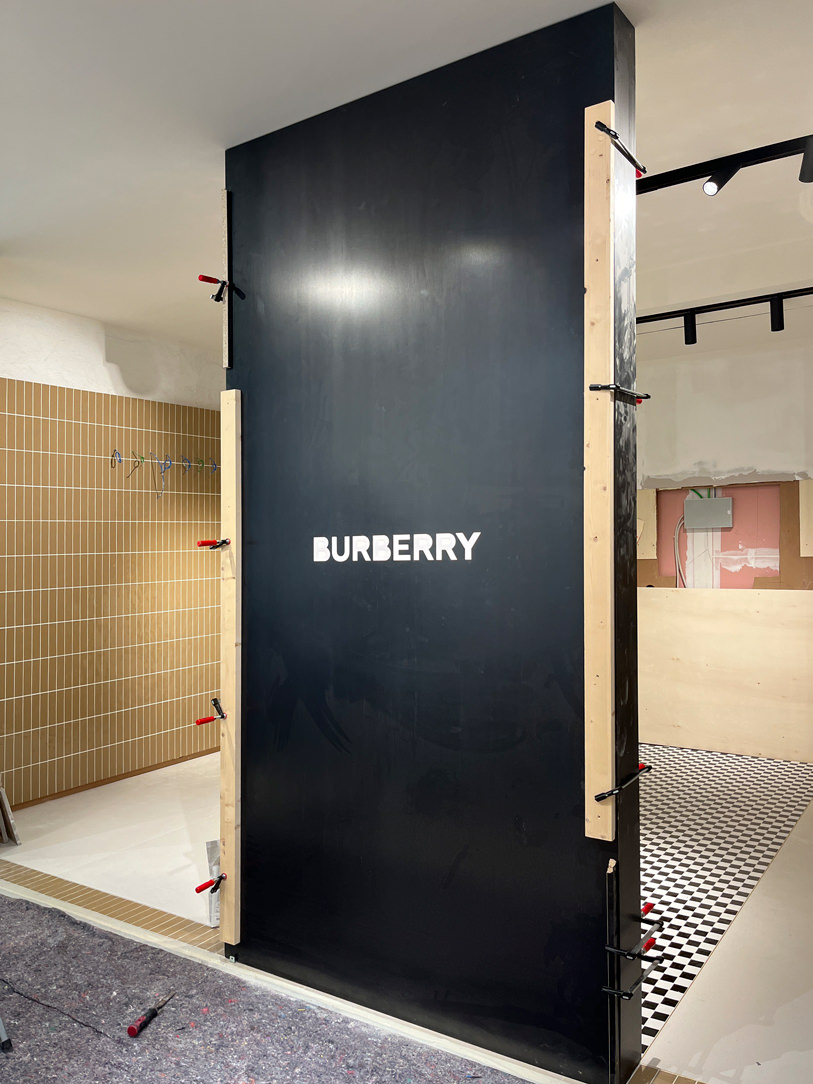
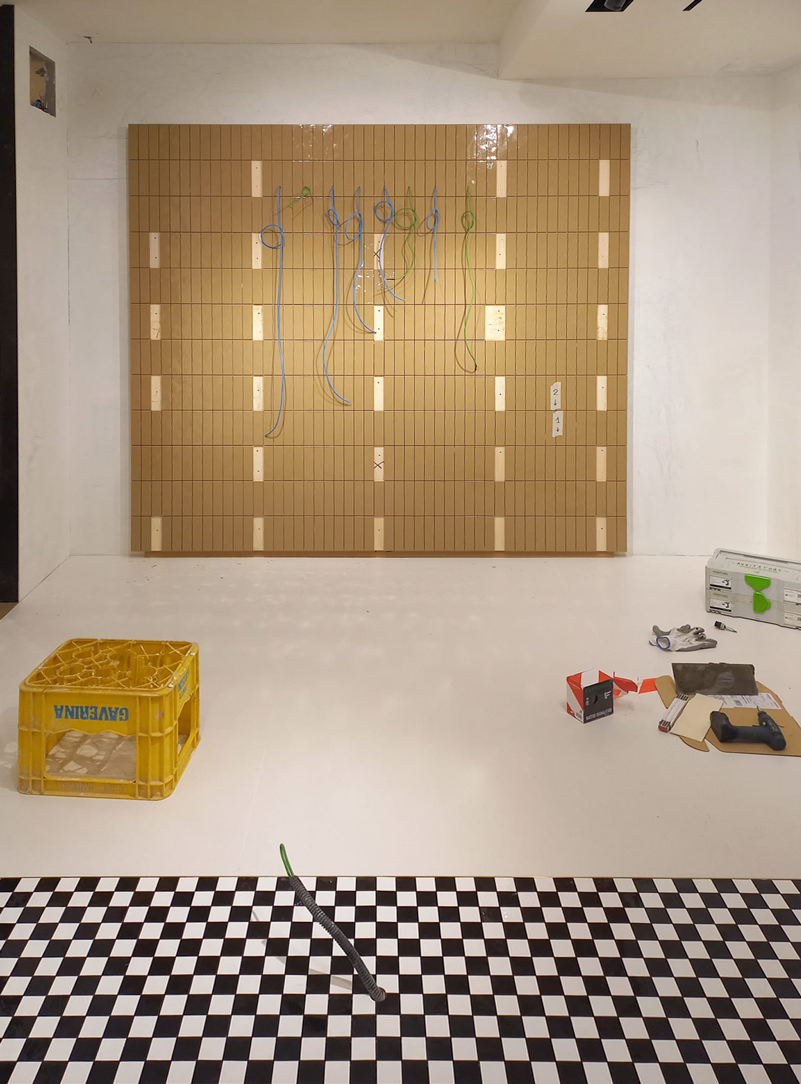
The second week was fully reserved to the Lisar Company, who installed the new custom-made furnishings.
Bronze hangers recall the profiles of the central display cabinet, the backlit shelves and the baseboards on the ground.
The white furniture with some hints of color links the bronze with the beige and monochrome tiles in an elegant and austere way are best reflecting the British spirit of the Brand.
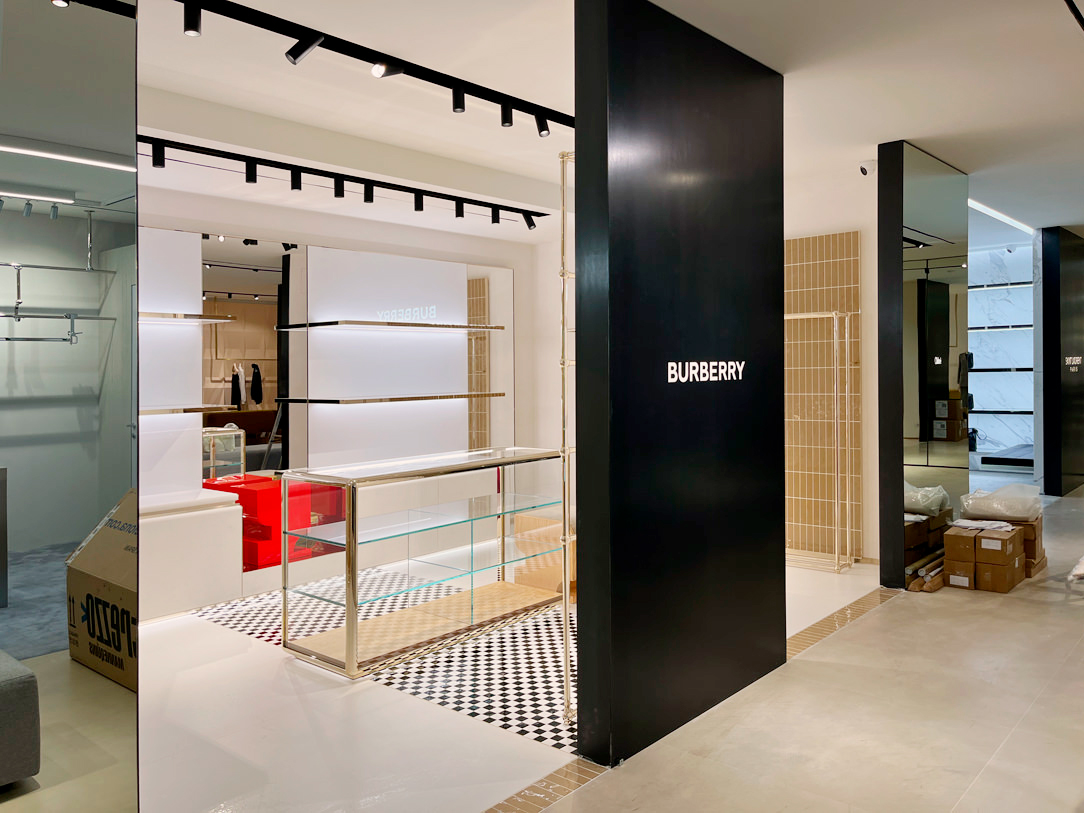
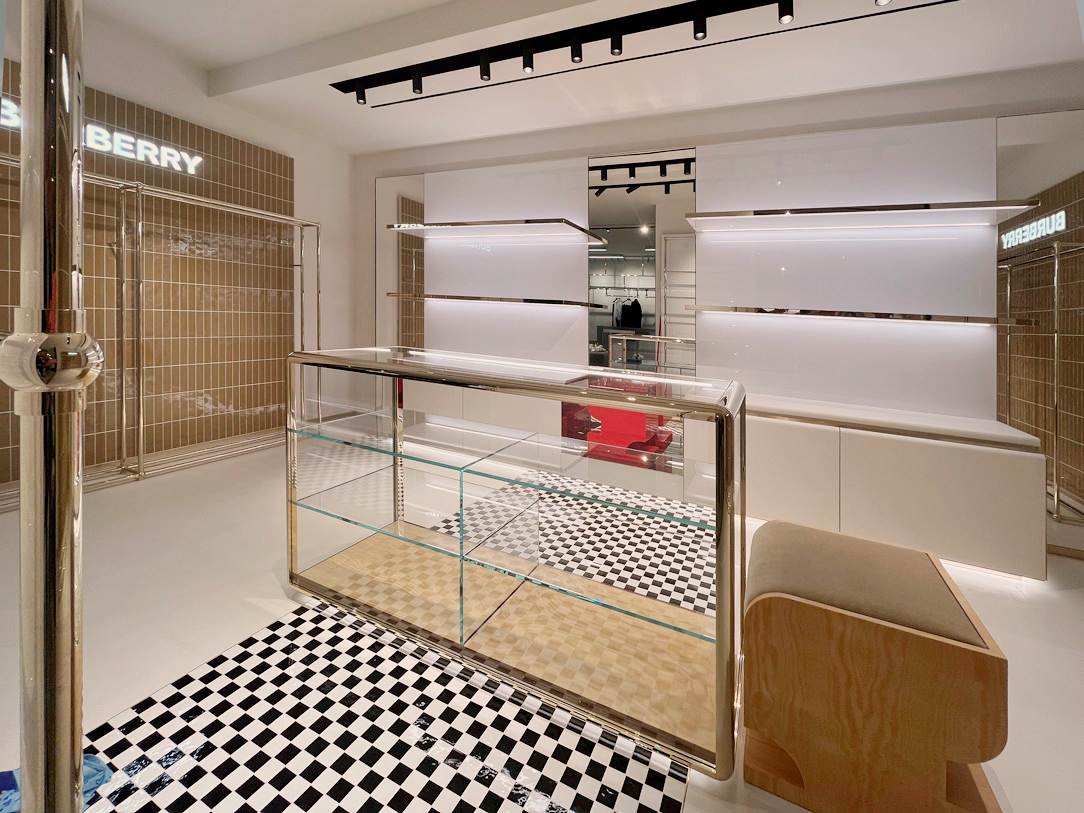
At the end of our time schedule, the last day was dedicated to supervision by Burberry, who checked the smallest detail and gave the green light to the inauguration of the space.
Here are the photos of the Burberry Corner, inaugurated in less than two weeks, after the intervention of the Visual Designers who exhibited the garments in an impeccable way.
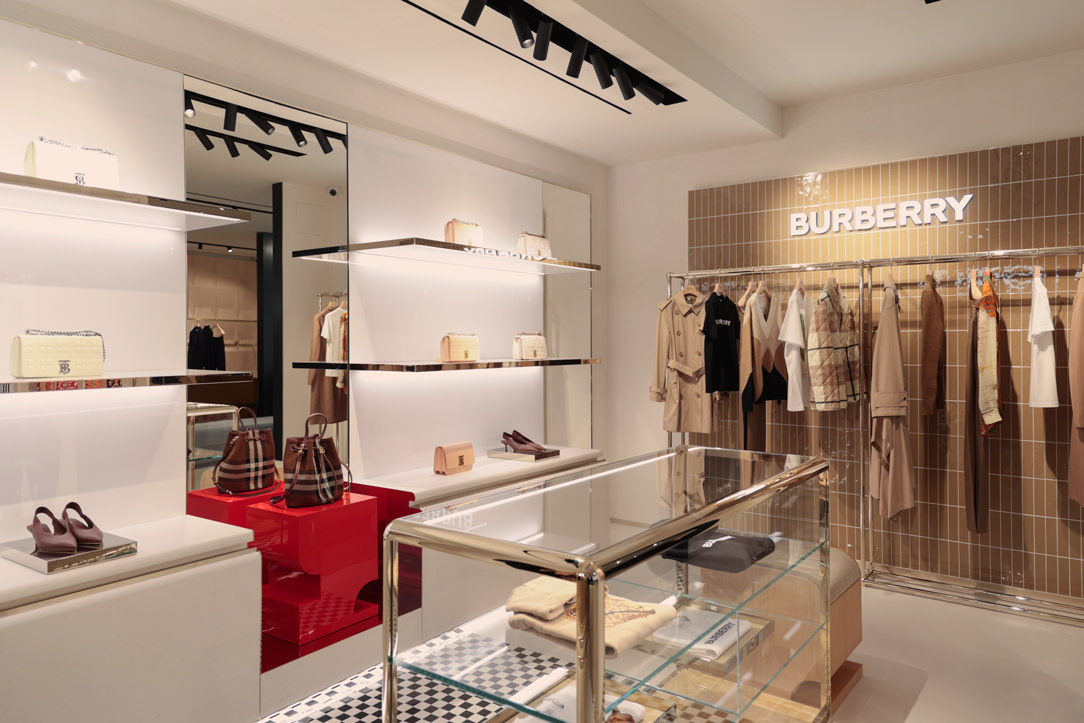
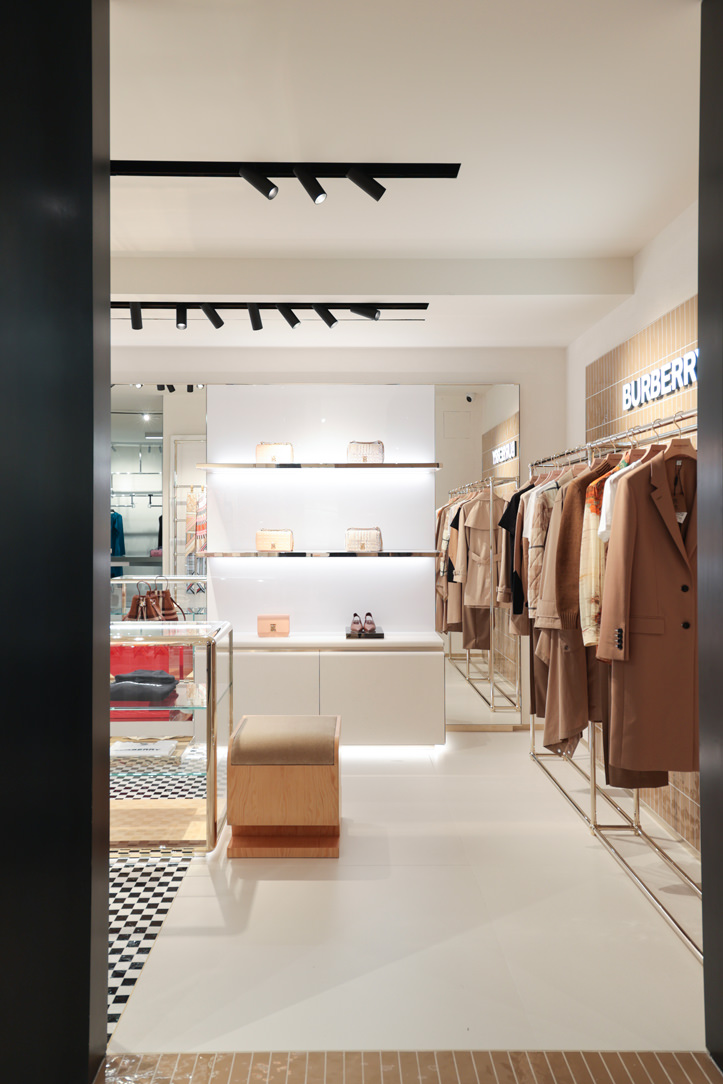
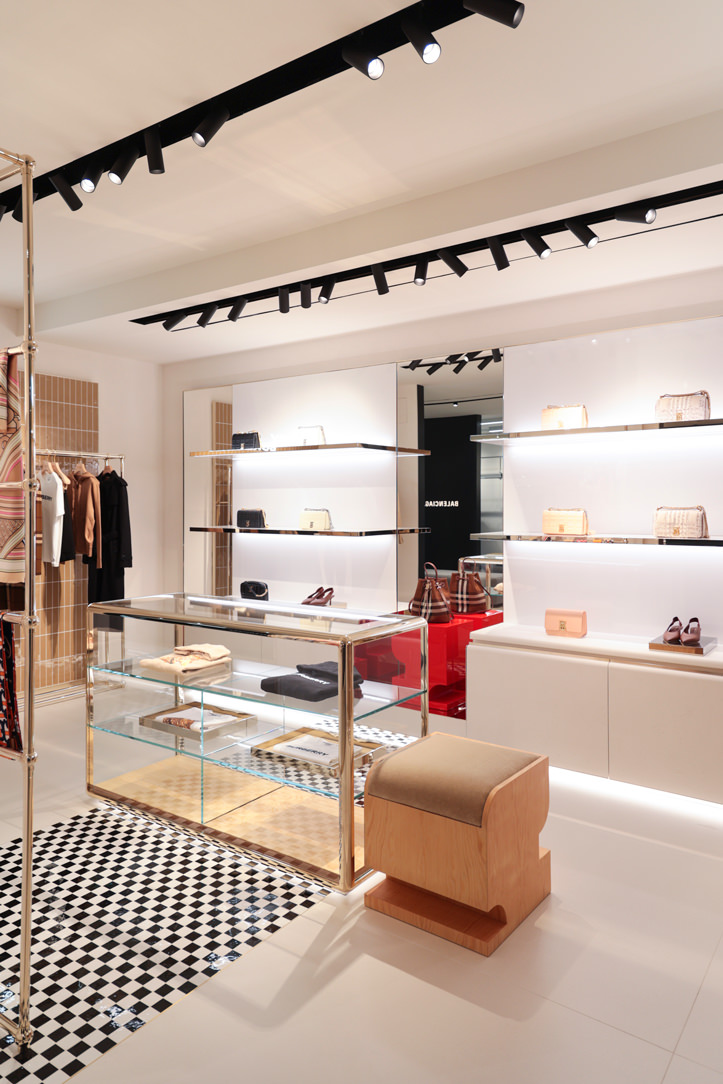
At this link the old article of the Tiziana Fausti shop’s Corners, in which Stella McCartney is present, if you want to compare the differences with the new space set up.